OUR EXPERIENCE
With leadership in the test and automation industry since 1999, our team of experts, have backgrounds from top electronics, defense and manufacturing solution vendors.
Although we have seen a wide gamut of challenges we understand that your most challenging manufacturing problems are unique to you or have unique requirements for your products. We have an experienced staff with multiple disciplines that can relate your problem to solutions we have worked on before, but give you the custom solutions giving you an edge in solving your challenges. Let our experience work for you and get you to a better solution faster.
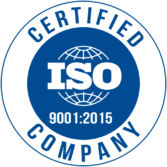
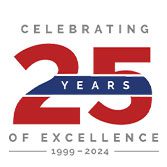
Working with ARC
WHAT TO EXPECT
For over a decade, ARC has been providing technical productivity solutions in automated test equipment (ATE) and torque assembly to a vast range of customers. Our team at ARC has the unique ability to analyze and fully understand the architecture of our customers’ technical product or manufacturing assembly. Our most successful functional test development and assembly solution efforts are the result of our existing and continuously growing expertise coupled with our ability to become as knowledgeable of the customer’s products as the customer’s own design engineers themselves. ARC is the only technical solution provider that blends these two critical needs.
Sales Process
Project Manager
ARC shall submit a project schedule to the Buyer. As a minimum, the project schedule must include all deliverables as defined in this SOW. The project schedule and associated progress shall be discussed and updated as part of the weekly status reviews.
Meeting and Reviews
Quality
ARC is ISO 9001:2015 registered.
Meet the ARC Leadership Team
As a veteran-owned business, ARC takes great pride in the relationships we have forged and solutions we are delivering for our customers.
Our leadership team is driven by you – we serve you, and we want to hear from you to make our solution and service oriented approach to problem solving work for you.
Garrett Partridge
CEO
ARC has grown significantly over the years, expanding our capabilities and support for our customers. Garrett previously worked with ARC from 2009 to 2018. He was our Operational Director during our largest growth period. Throughout his time here his responsibilities quickly increased, helping ARC expand our technical and operational capability. He has intimate knowledge of our operations, people, products, and vision.
Garrett most recently comes with professional director-level experience from GEFRAN, a global corporation specializing in precision measurement and automation control equipment. He was responsible for the entire North America Operations team including Production, Purchasing, Logistics, Technical Support, and Customer Support. During his time, he completely overhauled the customer support process to improve the customer experience, including the design and implementation a real-time customer portal, improved customer response time, reduced lead times, and expanded local production with the addition of a new facility. Most recently he developed a strategy for inventory control during the pandemic to ensure adequate supply of material and reduced lead times despite significant material supply challenges. His experience with international product development, customer-centric focus, and LEAN manufacturing are critical to expanding ARC’s efficiency and global reach.
Rob Nichols
Chairman of the Board
Rob has been a valued leader with ARC since 2002, joining as a systems engineer and then growing to VP of engineering, Sr. Program Manager, CEO and eventually Chairman of the Board. Rob moved into the CEO role in 2015 and was a visionary to lead our company in developing sophisticated productivity solutions in the areas of torque, assembly, test and automation. Rob has been a key facilitator in sales, manufacturing and finance teams to make ARC successful. In 2021, Rob accepted a new role as Chairman of the Board. In this new position, Rob has been able to expand his global strategic contribution.
Tim Vrettos
Director of Quality Assurance and Process Excellence
Tim Vrettos is a highly experienced Quality Manager with over 17 years in the field, specializing in continuous improvement and maintaining elevated standards of product and service quality across diverse sectors. He possesses a robust background in Quality Management Systems, lean manufacturing methodologies, and Defense Manufacturing, demonstrating a proven track record of enhancing organizational processes, optimizing costs, and facilitating customer satisfaction.
Beginning his career as a Manufacturing Engineer in multiple industries, Tim transitioned to Quality as a Quality Mission Operations (QMO) Engineer at Elbit Systems of America in 2007. He achieved his ASQ Quality Engineer certification in 2013, followed by obtaining his Six Sigma Black Belt certification from ASQ in 2018. In 2020, he advanced to the role of Quality Manager at Clear Align, where he successfully led initiatives to secure AS9100 recertification.
Tim joined ARC Technology Solutions in April 2024 as the Quality Manager. In this role, he prioritized improving the customer acceptance rate of ARC’s products and effectively managing supplier relationships. Due to his extensive experience, he was swiftly promoted to Director of Quality Assurance and Process Excellence, enabling him to have a more significant impact on the organization. He is leading the company’s initiative to align with the AS9100 Quality Management specification, with the ultimate goal of achieving AS9100 certification.
Ken Collins
Lead Technical Consultant
Ken has worked in many industries, first at Raytheon, assisting with creating depot repair solutions, then with IE Test back in the late 1990s. Joining ARC in 2002, Ken has led many of ARC’s engineering efforts for depot repair solutions and in creating the MSAT (Mixed Signal Automated Test) platform that has been adopted in both depot repair and in critical circuit card testing applications. Ken was President of ARC from 2008 to 2015, and most recently Ken has taken Engineering lead on critical architectures for our Digital System X (DSX) platform to quickly enable technology replacement by using modern FPGA architecture being at the core of both test and embedded designs.
John Pimental
Operations Consultant
John has led ARC in various roles and was President of the company through 2008. John, also a veteran, is currently supporting our manufacturing operations, working closely with sales, production support and manufacturing, to help drive successful manufacturing out of ARC.
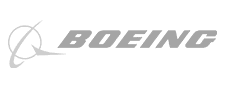
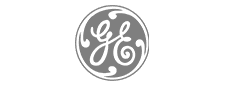
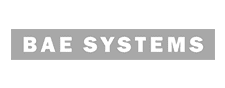
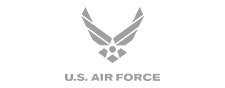
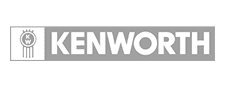
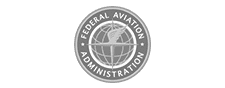
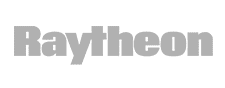
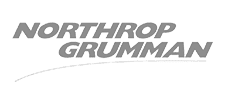
WHAT OUR CUSTOMERS ARE SAYING
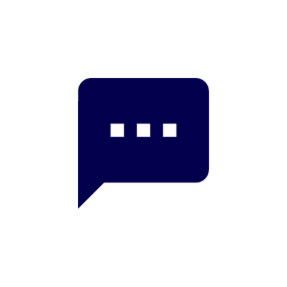
“I found ARC to be very professional and extremely helpful throughout the project, from specification, through design and execution. The final project was as expected. I would definitely work with ARC again.”
Mike K. - Associate Scientist
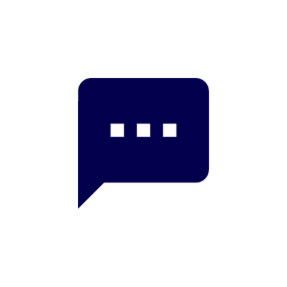
“I have been working with ARC for 3 years. Having had experience with other companies in the out-source model, I have found that ARC is an order of magnitude more capable and responsive to my requirements.”
Dean B. - Operations Test Engineering Manager
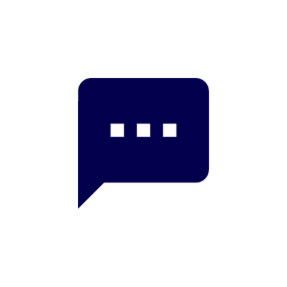
“ARC had built circuit boards for us in the January time-frame. Both of them came out perfect. These were complicated boards with fine pitches between some of the leads, in addition to having some specialty components. There were no misplaced components; nor any bad solder joints or solder splashes. I certainly appreciate the quick turn-around that you gave us (as well as the additional help that your crew gave us to straighten out our parts list). I appreciate good workmanship and the pride ARC takes to create a quality output. It is obvious that your company clearly has a good process and good workers. Again thanks for all the help and exceptional work.”
ANONYMOUS - Program Engineering Manager
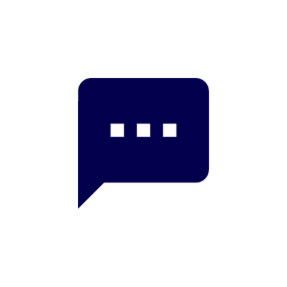
“Working with ARC Technology Solutions has been a great experience for us overall. We came to ARC with a tight development time frame to design and manufacture a test system. Their engineering team exceeded all of our requirements and expectations in developing the system in record timing. The program management and engineering group were always available for questions and kept us informed regarding the progress of our project. ARC has demonstrated, several times over, their ability to take a project from concept through design and layout and into production. ARC has provided us with excellent customer service and results. I look forward to the next opportunity to work with ARC Technology Solutions.”
VIMAL P - Electrical Engineer
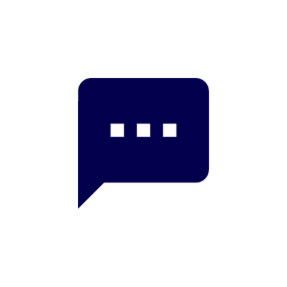
“Working at ARC Technology Solutions, LLC as an engineer offers many exciting challenges in creating the best solutions to complex problems. It requires close collaboration and clear communication with customers, suppliers, and fellow engineers; therefore, teamwork is a key ingredient. Our engineers work with the most interesting and like-minded professionals in electrical, mechanical and software engineering. This company is a project-based company; therefore, you get to tackle real problems and find the best solutions. The world changes constantly; as does engineering. Every working day or project is different which means the engineer is constantly learning interesting techniques and designs. You might be helping to build high efficiency tooling for aero engines, radar surveillance, software, or manufacturing process verification systems. Here at ARC, opportunities to make a positive difference to the world are endless.”
- Working as an Engineer at ARC
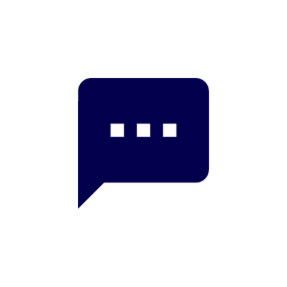
“Working at ARC Technology Solutions, LLC as a Salesperson offers a wide variety in your day-to-day activities. This diversity is one of the main reasons why a career at this company in sales can be exciting. Team members regularly engage with different types of people, analyze emerging market needs, and propose ingenious solutions to different problems. We work with our customers to improve their businesses with custom solutions. This variety puts the salesperson in front of many different people within the company. You rarely get the same day twice, and each department will have different needs and priorities. Selling for ARC involves solving problems on the spot and brings the satisfaction of being accountable for overseeing each customer’s problem from start to finish. While everyone else in your company may be debating the pros and cons of empowerment, you are living it.”
- Working as a Salesperson at ARC
How Can Our Flexible Approach Help You?
For a free assessment of your current engineering challenge.